Sifat material memainkan peran penting dalam mempengaruhi efisiensi aliran cetakan injeksi kemasan makanan dan minuman membuat. Efisiensi aliran mengacu pada seberapa baik bahan plastik cair mengalir ke dalam rongga cetakan dan mengisinya dengan benar selama proses pencetakan injeksi. Sifat material yang berbeda dapat mempengaruhi aspek ini dengan berbagai cara. Begini caranya:
1. Laju Aliran Leleh (MFR) atau Indeks Aliran Leleh (MFI):
- Dampak terhadap Efisiensi Aliran: Material dengan nilai MFR atau MFI yang tinggi memiliki kemampuan mengalir yang lebih besar, yang berarti material tersebut dapat mengalir lebih mudah ke dalam rongga cetakan. Hal ini menguntungkan untuk desain cetakan yang rumit atau rumit yang memerlukan kemampuan aliran yang baik untuk mengisi semua fitur cetakan secara efektif.
2. Viskositas:
- Dampak pada Efisiensi Aliran: Viskositas adalah ukuran ketahanan suatu material terhadap aliran. Bahan dengan viskositas rendah mengalir lebih mudah, sedangkan bahan dengan viskositas tinggi mengalir lebih lambat. Bahan dengan viskositas rendah dapat mengisi rongga cetakan lebih cepat dan dengan tekanan lebih kecil, sehingga meningkatkan efisiensi aliran. Bahan dengan viskositas tinggi mungkin memerlukan tekanan injeksi yang lebih tinggi dan waktu pengisian yang lebih lama.
3. Suhu Bahan:
- Dampak pada Efisiensi Aliran: Suhu material selama pencetakan injeksi sangat penting. Temperatur yang lebih tinggi mengurangi viskositas material, membuatnya lebih mudah mengalir. Namun, panas berlebih dapat menyebabkan degradasi atau lengkungan. Kontrol suhu yang tepat sangat penting untuk mengoptimalkan efisiensi aliran.
4. Pengisi dan Penguat:
- Dampak pada Efisiensi Aliran: Bahan dengan bahan pengisi (misalnya serat kaca) atau penguat mungkin mempunyai sifat aliran yang berubah. Aditif ini dapat mempengaruhi perilaku aliran material, sehingga perlu dilakukan penyesuaian parameter proses untuk memastikan pengisian cetakan yang tepat.
5. Daktilitas dan Fleksibilitas Material:
- Dampak pada Efisiensi Aliran: Bahan ulet dan fleksibel dapat beradaptasi dengan geometri cetakan yang kompleks dengan lebih mudah, sehingga meningkatkan efisiensi aliran dalam desain yang rumit. Bahan yang rapuh mungkin kesulitan mengisi fitur cetakan tanpa cacat.
6. Kepadatan Bahan:
- Dampak pada Efisiensi Aliran: Kepadatan material dapat mempengaruhi efisiensi aliran sampai batas tertentu. Bahan dengan kepadatan lebih rendah mungkin lebih mudah dikompresi dan dapat menghasilkan aliran yang lebih baik ke dalam fitur cetakan. Namun, material dengan kepadatan lebih tinggi dapat memberikan kekuatan struktural yang lebih baik.
7. Konduktivitas Termal:
- Dampak pada Efisiensi Aliran: Konduktivitas termal material dapat mempengaruhi laju pendinginan setelah injeksi. Pendinginan yang cepat dapat mengeraskan material sebelum waktunya, sehingga mempengaruhi efisiensi aliran. Penting untuk menyeimbangkan laju pendinginan untuk memastikan pengisian penuh.
8. Sifat Reologi Bahan:
- Dampak pada Efisiensi Aliran: Sifat reologi, seperti laju geser dan tegangan geser, menggambarkan perilaku material dalam kondisi aliran yang berbeda. Bahan dengan perilaku penipisan geser yang baik menunjukkan peningkatan efisiensi aliran karena bahan tersebut menjadi kurang kental pada laju geser yang lebih tinggi.
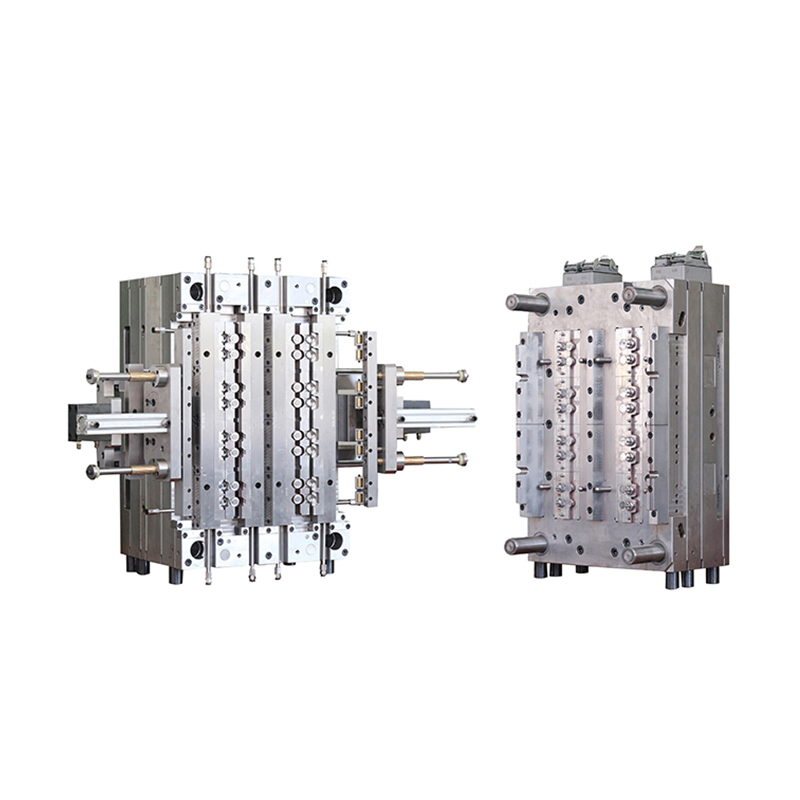
9. Bahan Spesifik (misalnya, Amorf vs. Kristal):
- Dampak pada Efisiensi Aliran: Sifat spesifik material, baik amorf atau kristal, dapat mempengaruhi perilaku alirannya. Bahan amorf cenderung memiliki aliran yang lebih seragam dan isotropik, sedangkan bahan kristal mungkin menunjukkan karakteristik aliran terarah.
10. Kecenderungan Warpage Material:
- Dampak pada Efisiensi Aliran: Material yang rentan melengkung selama pendinginan mungkin memerlukan laju injeksi yang lebih lambat atau kontrol suhu yang lebih hati-hati untuk mencegah gangguan aliran yang menyebabkan lengkungan.
Mengoptimalkan efisiensi aliran dalam pembuatan cetakan injeksi kemasan makanan dan minuman melibatkan pemilihan bahan dengan kombinasi sifat yang tepat untuk desain cetakan tertentu dan persyaratan produksi. Hal ini juga memerlukan kontrol yang tepat terhadap parameter proses, seperti suhu dan kecepatan injeksi, untuk memastikan material mengalir secara seragam dan mengisi rongga cetakan sepenuhnya tanpa cacat. Selain itu, desain cetakan memainkan peran penting dalam memandu aliran material untuk pengisian yang efisien dan seragam.