Mengoptimalkan ukuran gerbang dan lokasi dalam cetakan injeksi pompa lotion melalui analisis aliran cetakan melibatkan proses simulasi, analisis, dan penyesuaian desain yang sistematis. Berikut panduan langkah demi langkah untuk mencapai pengoptimalan ini:
1. Tentukan Tujuan dan Kriteria Proyek:
- Mulailah dengan mendefinisikan secara jelas tujuan dan kriteria cetakan injeksi pompa lotion. Pertimbangkan faktor-faktor seperti kualitas komponen, waktu siklus, penggunaan material, dan kendala biaya.
2. Kumpulkan Data Material:
- Dapatkan data material yang akurat untuk resin plastik spesifik yang akan digunakan dalam proses pencetakan injeksi. Ini termasuk indeks aliran leleh (MFI), viskositas, sifat termal, dan karakteristik material lainnya.
3. Pembuatan Model:
- Buat model 3D detail bagian pompa lotion dan cetakan injeksi, termasuk rongga, inti, saluran pendingin, dan sistem runner. Pastikan model secara akurat mewakili kondisi produksi yang diinginkan.
4. Pengaturan Simulasi:
- Memanfaatkan perangkat lunak analisis aliran cetakan untuk mengatur simulasi. Tentukan parameter proses pencetakan injeksi, seperti tekanan injeksi, profil suhu, dan laju pendinginan. Tentukan lokasi gerbang dan ukuran gerbang awal.
5. Jalankan Simulasi Awal:
- Jalankan simulasi aliran cetakan awal dengan lokasi dan ukuran gerbang yang dipilih. Analisis hasilnya, termasuk waktu pengisian, distribusi tekanan, garis las, dan lokasi perangkap udara. Identifikasi potensi masalah atau area yang perlu diperbaiki.
6. Analisis Lokasi Gerbang:
- Evaluasi kesesuaian lokasi gerbang yang dipilih. Pertimbangkan faktor-faktor seperti pengisian rongga yang seimbang, penghindaran cacat kosmetik, dan meminimalkan dampak garis las. Sesuaikan lokasi gerbang sesuai kebutuhan.
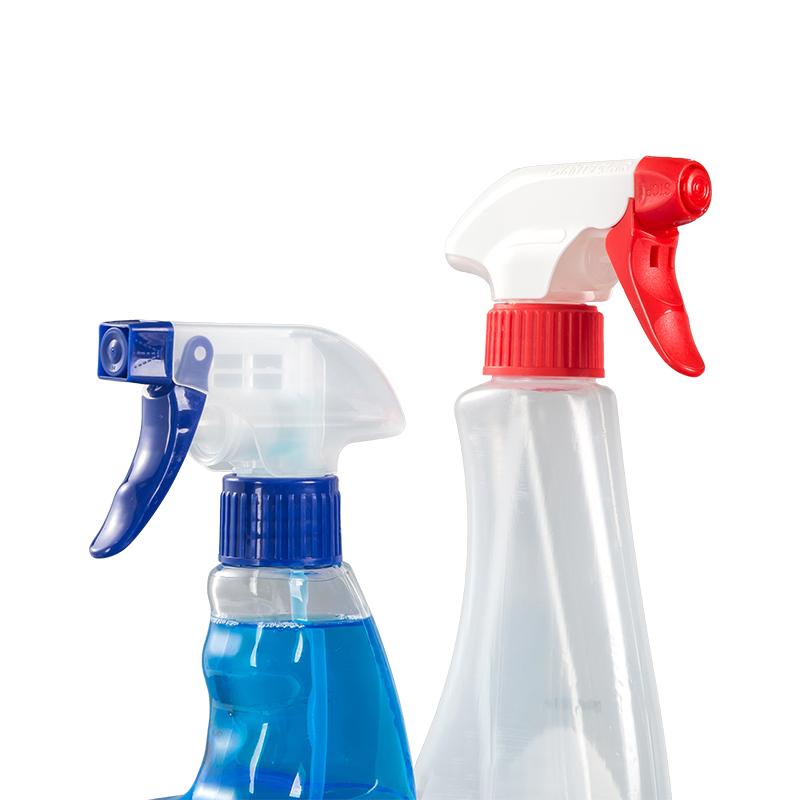
7. Analisis Ukuran Gerbang:
- Menganalisis pengaruh ukuran gerbang pada proses injeksi. Tingkatkan atau kurangi ukuran gerbang secara bertahap dalam simulasi berikutnya untuk menemukan ukuran optimal yang menyeimbangkan waktu pengisian, tekanan, dan aliran material tanpa menyebabkan cacat.
8. Pemilihan Tipe Gerbang:
- Tergantung pada hasil analisis ukuran gerbang, pilihlah jenis gerbang yang sesuai, seperti gerbang sprue, gerbang tepi, atau gerbang kipas. Jenis gerbang mempengaruhi cara material memasuki rongga dan dapat mempengaruhi kualitas komponen.
9. Optimasi Sistem Pelari:
- Optimalkan desain sistem runner untuk memastikan distribusi material merata ke semua rongga. Sesuaikan dimensi dan konfigurasi runner untuk meminimalkan pemborosan material dan penurunan tekanan.
10. Analisis Saluran Pendingin:
- Menilai dampak lokasi dan ukuran gerbang terhadap efisiensi pendinginan. Pastikan konfigurasi gerbang yang dipilih tidak mengganggu efektivitas saluran pendingin. Sesuaikan penempatan saluran pendingin jika perlu.
11. Simulasi Iteratif:
- Lakukan simulasi berulang, lakukan penyesuaian bertahap pada lokasi dan ukuran gerbang berdasarkan hasil analisis. Terus perbaiki desain hingga kriteria yang diinginkan, seperti pengisian seimbang dan cacat minimal, terpenuhi.
12. Validasi Akhir:
- Melakukan analisis aliran cetakan akhir untuk memvalidasi ukuran dan lokasi gerbang yang dioptimalkan. Konfirmasikan bahwa desain memenuhi tujuan dan kriteria proyek yang telah ditentukan.
13. Dokumentasi dan Pelaporan:
- Dokumentasikan hasilnya, termasuk konfigurasi gerbang yang dipilih, data simulasi, dan penyesuaian desain apa pun. Siapkan laporan yang merangkum proses optimasi dan hasilnya.